Customization
Scope of customization:
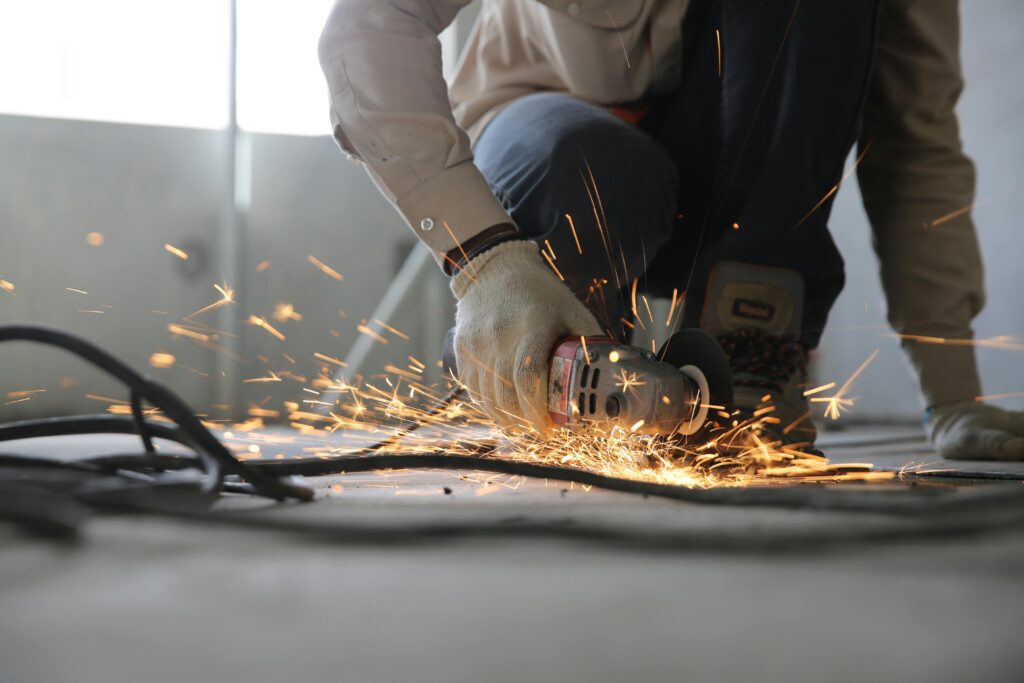
Thermal & EMI solutions
There are times when standard products may not meet your requirements for various reasons—whether due to a unique product design, excessive cost, overly complex features, or simply because a tailored solution is needed. In some cases, no standard product exists that fits your needs, and custom designs become necessary. Whatever the reason, we understand the importance of finding cost-effective and efficient solutions.
At GBA, our custom project team is dedicated to addressing these “customization” needs. While we cannot guarantee that every requirement will be met, we are committed to collaborating closely with our customers to develop tailored solutions that work. We’re always striving to find better products and more affordable options that align with your specific needs.
What GBA can offer: GBA’s 3 main advantages
A: Expertise in Small Batch Orders
GBA excels in small batch and prototype production, offering a flexible and versatile etching process using universal tools and machines. This capability allows for quick turnaround and customization, especially beneficial for early-stage product development and low-volume production runs.
B: Comprehensive Manufacturing Capabilities
GBA possesses full manufacturing capabilities, including the design and creation of tools using CAD, CAM, and high-precision Wire EDM technology. We can customize a wide range of components, including connectors, switches, and electronic accessories. Additionally, we can quickly complete electroplating processes, such as gold, zinc, and copper plating. GBA serves globally recognized companies in telecom, automotive, and medical sectors, providing high-quality, non-standard stamping applications.
C: High-Standard Quality Control and Rapid Process Capabilities
GBA follows a precise production schedule and utilizes Statistical Process Control (SPC) methods to ensure stringent quality control during both mass production and prototyping. As a result, leading enterprises choose GBA as a trusted partner for their customized product needs.
GBA’s Process Capabilities:
- Fully Automatic or Semi-Automatic Equipment: Advanced machinery to support various production needs.
- Ultrasonic Welding: Ensuring strong, durable bonds for specialized applications.
- Conventional and Special Riveting: Custom riveting solutions for unique designs and requirements.
- Meeting Harsh Technical Requirements: Capabilities to handle tough, demanding conditions in product manufacturing.
- Special Packaging Solutions: Tailored packaging for optimized assembly and storage.
- Precision Engraving/Laser Engraving Machines: High-precision marking and engraving for customization needs.
NON-STANDARD REQUIREMENTS
GBA can quickly support the design and manufacturing of non-standard products. The three main categories of non-standard requirements are:
A: Early-Stage Design Validation
A sample is produced to validate new design concepts or processes before full-scale production.
B: Issue Resolution in Mass Production
When problems arise during mass production, GBA can add or modify products to resolve issues and ensure production continuity.
C: Special Structural or Assembly Adjustments
For unique assembly methods or spatial requirements where standard parts cannot be used, GBA can adjust or customize parts to meet these specific needs.
SURFACE TREATMENT
Surface treatment is an essential process across industries, from traditional to high-tech sectors, and for materials ranging from metals to plastics and non-metallic surfaces. This process enhances base materials by making them corrosion-resistant, wear-resistant, and heat-resistant, ultimately extending their lifespan. Surface treatment also improves the physical, mechanical, and cosmetic properties of the material, thereby increasing the product’s value and performance. These processes are collectively referred to as surface treatment or surface finishing.