EF-series | Conductive FIP Gasket
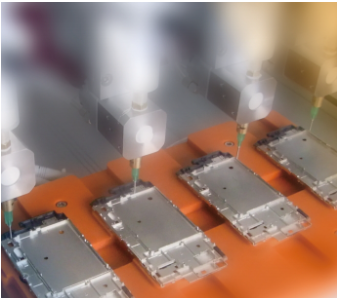
Product Highlights
- Shielding effectiveness 90dB to 110dB
- operating frequency: 200MHz to 20GHz
- curing modes: 150oC / 30min, 120oC / 120min, 25oC / 24hours
- Automatic dispensing, low tooling cost
- Bead cross section (mm): 0.3(h)x0.3(w) to 1.7(h)x2.5(w)
Product Applications examples:
- Communication equipment: Ensures reliable signal transmission and protection from EMI and environmental factors.
- Automotive electronics: Offers EMI shielding and Environmental sealing for automotive systems exposed to extreme temperatures and vibrations.
- Medical instruments: Protects critical medical devices from EMI and contamination, ensuring safe and reliable operation.
- I/O dust control: Seals I/O ports and connections against dust, moisture, and other contaminants, ensuring system reliability.
- Servers: Provides EMI shielding and dust protection, helping to maintain server performance and longevity in data centers and industrial settings.
The EF-series elastomers ensure that these applications remain functional, reliable, and efficient, even in challenging environments.
Descriptions:
The EF-series products described are highly specialized conductive elastomers designed for a range of demanding applications where electromagnetic interference (EMI) shielding and environmental sealing are critical. These materials are formulated with different types of conductive particles, which allow for a variety of applications depending on the specific needs of the project.
Key Features of the EF-Series Conductive Elastomers:
- Variety of Conductive Particle Formulations:
- The EF-series includes different conductive particle formulations (such as silver, nickel, aluminum, or carbon-based particles) that provide varying levels of shielding effectiveness. This allows the product to be tailored to different shielding requirements depending on the application.
- High and Room Temperature Vulcanization Options:
- The EF-series offers vulcanization options for room temperature or high-temperature curing. Vulcanization is a chemical process that improves the elastomer’s strength, elasticity, and durability, making it suitable for use in harsh environments.
- Adhesive and Molding Properties:
- Fluidity of Glue: The material has excellent fluidity, which makes it easy to apply via dispensing techniques, ensuring precise and efficient application in various processes.
- Adhesion: After vulcanization, the adhesive exhibits excellent adhesion to a variety of surfaces, including metals and plastics, ensuring strong and durable bonding.
- Wear Resistance: The product is designed to withstand repeated disassembly and reassembly, making it highly durable in applications that require frequent handling or maintenance.
- Low Compression Permanent Deformation: The material retains its shape and function, even after being compressed or subjected to mechanical stress, reducing the risk of permanent deformation.
- Applications:
- Optical Communication Modules: Essential for applications requiring both environmental sealing and EMI shielding in sensitive optical communication equipment.
- 5G Communication Base Stations: Ensures protection and shielding for high-speed communication infrastructure.
- Radar Equipment: Protects sensitive radar systems from environmental factors and electromagnetic interference.
- Automotive Electronics: Suitable for automotive systems requiring reliable shielding and environmental sealing, particularly in harsh automotive environments.
- Consumer Electronics: Provides EMI shielding and protection against environmental factors in consumer devices such as smartphones, laptops, and wearables.
Dispensing Structure Design Suggestions:
GBA offers professional support to help product designers optimize the dispensing path and dispensing section for efficient application. The dispensing structure design options cater to various product needs based on the size, shape, and requirements of the project.
- D Section:
- Aspect Ratio: 0.75:1
- Applications: Suitable for most dispensing products, offering a good balance of width and height for standard designs.
- △ Section (Triangular):
- Aspect Ratio: 1:1
- Applications: Ideal for products with limited width but requiring a certain height.
- Double D-Shaped Section:
- Aspect Ratio: ≥ 1:1
- Applications: Designed for products that require a larger height than width, allowing for greater flexibility in packaging and dispensing.
These design options ensure that the dispensing material is applied in the most efficient way possible, minimizing waste and maximizing performance.
Performance Testing Methods:
GBA provides comprehensive testing and quality control to ensure that products meet high standards for performance and reliability:
- Adhesion Test:
- Performed according to GBA’s internal standard QA-WI-FIP-002, with reference to HW DKBA04800202_FIP technical requirements. This test checks the bond strength of the adhesive to ensure long-lasting adhesion to various surfaces.
- Volume Resistivity Test:
- According to the MIL-DTL-83528C standard, this test measures the material’s resistance to electrical flow, ensuring it provides effective EMI shielding.
- High and Low Temperature Test:
- Also conducted according to MIL-DTL-83528C, this test ensures that the material maintains its integrity and performance across a wide range of temperatures, from low to high extremes.
- Shielding Effectiveness Test:
- Also performed in compliance with MIL-DTL-83528C, this test assesses the material’s ability to shield against electromagnetic interference, ensuring the product meets the required shielding performance for its intended application.
Summary:
The EF-series conductive elastomers offer a versatile and high-performance solution for a wide range of applications, from optical communication modules and 5G base stations to automotive electronics and consumer devices. These materials are designed to provide both electromagnetic shielding and environmental protection, with excellent adhesive properties, wear resistance, and low compression deformation. GBA’s comprehensive support, including dispensing structure design suggestions and extensive performance testing, ensures that these materials meet the highest standards of quality and reliability.
SPECIFICATIONS TABLE
Part Numbers | |||||||||||||
---|---|---|---|---|---|---|---|---|---|---|---|---|---|
Parameter | Test Method | Units of Measure | EF2111-20 | EF2120-20 | EF2121-10 | EF2125-10 | EF2310-10 | EF2510-10 | EF2511-10 | EF2610-10 | EF2611-10 | EF2610-20 | EF2610S-20 |
Characteristic | – | – | Super Soft | High Flow Rate | Super Soft | Superfine | Corrosion resistance | High Performance | Quick Surface Drying | High Resilience | Small Size | Low Temperature Fast Curing | |
Conductive Particles | – | – | Ni/C | Ni/C | Ni/C | Ni/C | Ag/Al | Ag/Cu | Ag/Cu | Ag/Ni | Ag/Ni | Ag/Ni | Ag/Ni |
Filler Material | – | – | Silicon Rubber | Silicon Rubber | Silicon Rubber | Silicon Rubber | Silicon Rubber | Silicon Rubber | Silicon Rubber | Silicon Rubber | Silicon Rubber | Silicon Rubber | Silicon Rubber |
Curing Conditions | – | – | High Temperature Curing | Room Temperature Curing | Room Temperature Curing | High Temperature Curing | |||||||
Curing Temperature | – | oC | 150 | 150 | 25 | 25 | 25 | 25 | 25 | 25 | 25 | 120 | 120 |
Curing Time | – | – | 30min | 30min | 24Hour | 24Hour | 12Hour | 24Hour | 12Hour | 24Hour | 24Hour | 2Hour | 2Hour |
Hardness (after cured) | ASTMD2240 | ShoreA | 45 | 60 | 45 | 45 | 60 | 60 | 55 | 50 | 50 | 55 | 50 |
Tensile Strength | ASTMD412 | PSI | 150 | 150 | 150 | 120 | 130 | 130 | 130 | 200 | 200 | 150 | 150 |
Ductility | ASTMD412 | /U | 100 | 100 | 100 | 100 | 180 | 150 | 150 | 100 | 180 | 100 | 100 |
Density | ASTMD792 | g/cm³ | 1.9 | 1.9 | 1.9 | 2.2 | 2.2 | 3.2 | 3 | 3.8 | 3.8 | 3.9 | 3.9 |
Volume resistivity | MIL-DTL-83528C | ohm-cm | 0.04 | 0.03 | 0.04 | 0.04 | 0.008 | 0.003 | 0.004 | 0.005 | 0.01 | 0.01 | 0.01 |
Compression Ratio 70 hours at 100 °C | ASTMD395-B | % | 30 | 30 | 30 | 30 | 30 | 30 | 30 | 30 | 30 | 30 | 30 |
Operating Temperature | – | ℃ | -55~+125 | -55~+125 | -55~+125 | -55~+125 | -55~+125 | -55~+125 | -55~+125 | -55~+125 | -55~+125 | -55~+125 | -55~+125 |
Flame Retardant Grade | UL94 | – | V-0 | V-0 | V-0 | V-0 | V-0 | V-0 | V-0 | V-0 | V-0 | V-0 | V-0 |
Shielding Effectivess | MIL-DTL-83528C | dB | >90 | >90 | >90 | >90 | >100 | >110 | >100 | >100 | >100 | >100 | >100 |
(AVG 200MHz~18GHz) | |||||||||||||
Adhesion Strength | QA-WI-054 | N/cm | >10 | >10 | >10 | >10 | >10 | >10 | >10 | >10 | >10 | >10 | >10 |
@bead size w1.1xh0.9xl10mm | |||||||||||||
Rebound force @30% compression | QA-WI-058 | N/cm | 20 | 43 | 21 | 14 | 35 | 39 | 40 | 25 | 19 | 28 | 28 |
@ bead size | |||||||||||||
w1.1xh0.9xl10mm | |||||||||||||
Bead Size | Width x Height | mm | 0.7*0.5/ | 0.7*0.5 | 0.5*0.35/ | 0.35*0.35/ | 0.6*0.4/ | 0.5*0.35/ | 0.5*0.35/ | 0.5*0.35 | 0.3*0.3/ | 0.5*0.35 | 0.5*0.35/ |
Minimum/Maximum Recommended Value | 2.5*1.7 | 2.5*1.7 | 2.5*1.7 | 2.5*1.7 | 2.5*1.7 | 2.5*1.7 | 2.5*1.7 | 2.5*1.7 | 2.5*1.7 | 2.5*1.7 | 2.5*1.7 | ||
Effective Storage Time | – | Month | 6 | 6 | 3 | 3 | 3 | 3 | 3 | 3 | 3 | 6 | 6 |
Storage Temperatures | – | oC | -30~-10 | -30~-10 | -30~-10 | -30~-10 | -30~-10 | -30~-10 | -30~-10 | -30~-10 | -30~-10 | -30~-10 | -30~-10 |