CF-series | Co-extruded EMI & Environmental Elastomer
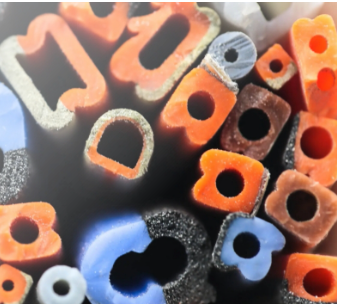
Product Highlights
- The conductive and non-conductive layers are co-extruded, integrating electrical and environmental sealing.
- Environmental seal withstand extreme temperature ranges -55ºC to +170ºC.
- Excellent mechanical properties, soft and high resilience.
- ideal for use in automotive, aerospace applications
Applications:
- Automotive Industry:
- This elastomer is perfect for use in automotive seals, connectors, and gaskets where both environmental sealing and electrical shielding are necessary to protect sensitive electronics from the elements and interference.
- Aerospace and Military:
- The material’s high temperature resistance and resilience make it ideal for aerospace and military applications, where components are subjected to extreme temperatures and harsh environments.
- Industrial Equipment:
- In heavy-duty machinery and industrial equipment, where both environmental protection and electrical shielding are needed to ensure safe and reliable operation in dust-filled or wet environments.
- Consumer Electronics:
- It can be used in outdoor electronics or any devices that need to be resistant to dust and water ingress while still providing electrical shielding for signal integrity.
Product Descriptions :
The co-extruded conductive elastomer is a highly specialized material that combines both conductive and non-conductive silicone elastomers in a single, precisely engineered product. By using a specialized extrusion process, this material achieves high performance in both shielding effectiveness and environmental protection, making it ideal for a wide range of demanding applications.
Key Features of Co-Extruded Conductive Elastomer:
- Conductive and Non-Conductive Layers: The co-extrusion process combines two distinct types of silicone elastomers – one conductive and one non-conductive – allowing the material to provide both electrical shielding and environmental sealing in a single product. The conductive part shields against electromagnetic interference (EMI) or radio frequency interference (RFI), while the non-conductive portion offers waterproofing and dust-proofing capabilities.
- Shielding Effectiveness: The conductive part of the elastomer ensures that the material provides excellent shielding effectiveness, which is essential for applications in sensitive electronics, ensuring that electromagnetic fields (EMF) do not interfere with the device’s performance.
- Environmental Protection (IP68 Rating): With the correct groove size design, the product can achieve an IP68 protection rating, ensuring complete protection against dust ingress and the ability to withstand immersion in water. This makes it highly suitable for use in harsh environmental conditions, such as outdoor or underwater applications.
Categories of Co-Extruded Conductive Elastomer:
- CF2310 (Ag/Al + Silicone Elastomer Co-Extrusion):
- Composition: Silver (Ag) and Aluminum (Al) conductive particles combined with silicone elastomer.
- Applications: Suitable for general shielding and sealing applications, providing a good balance of conductivity and cost.
- CF2110 (Ni/C + Silicone Elastomer Co-Extrusion):
- Composition: Nickel (Ni) and Carbon (C) conductive particles combined with silicone elastomer.
- Applications: This material is ideal for situations where cost-effectiveness is a priority while still needing good conductive properties.
- CF2410 (Ag/Glass + Silicone Elastomer Co-Extrusion):
- Composition: Silver (Ag) and Glass (Glass) conductive particles combined with silicone elastomer.
- Applications: Provides high shielding effectiveness while maintaining good mechanical properties. The glass particles may enhance thermal stability and mechanical strength.
- CF2320 (Ag/Al Fluorosilicone + Silicone Elastomer Co-Extrusion):
- Composition: Silver (Ag) and Aluminum (Al) particles in a fluorosilicone matrix combined with silicone elastomer.
- Applications: Ideal for harsh environments, particularly in aerospace or automotive sectors where both high shielding and excellent chemical resistance are required.
Additional Considerations:
- PSA Option for Co-Extrusion Strips:
- Co-extruded strips can come with a Pressure Sensitive Adhesive (PSA) option, which allows them to be easily applied to various surfaces without the need for additional adhesives. However, it’s important to note that the presence of adhesive and a release liner will affect the length tolerance of the product. The dimensional tolerances will relax when the PSA is applied, but once the protective liner is removed, the final product dimensions will return to their original specifications.
- Installation Directions:
- Co-extrusion strips are directional when installed in grooves. This means that the non-conductive portion should face outward to ensure that it creates a waterproof and dust-proof seal. On the other hand, the conductive portion should face inward, in contact with the metal covers, to form a continuous electrical path, ensuring effective grounding and shielding.
Summary:
The co-extruded conductive elastomer is a highly versatile material designed for electromagnetic shielding, environmental sealing, and customizable applications. By combining conductive and non-conductive properties, it offers dual functionality: protecting sensitive electronic components from interference while also providing robust environmental protection. Depending on the specific conductive particles used (Ag/Al, Ni/C, Ag/Glass, or Ag/Al fluorosilicone), the material can be tailored to meet different levels of shielding effectiveness, mechanical properties, and resistance to harsh environmental conditions. The addition of PSA for easy installation and the ability to restore dimensional tolerances after removing the liner further enhances the material’s practicality for various applications.
SPECIFICATIONS TABLE
CF Material # | CF2110 | CF2310 | CF2320 | CF2410 | TEST METHOD | ||||
Substrate | Conductive Elastomer | Silicone | Conductive Elastomer | Silicone | Conductive Elastomer | Fluorosilicone | Conductive Elastomer | Silicone | N/A |
EC2110 | NC1010 | EC2310 | NC1010 | EC2320 | NC1020 | EC2410 | NC1010 | ||
Conductive Particles | Ni/C | N/A | Ag/Al | N/A | Ag/Al | N/A | Ag/G | N/A | N/A |
Density (g/cm³) | 1.9 | 1.2 | 2.2 | 1.2 | 2.2 | 1.2 | 2.0 | 1.2 | ASTM D792 |
Volume Resistivity (Ω·cm) | 0.1 | N/A | 0.008 | N/A | 0.012 | N/A | 0.006 | N/A | MIL-DTI- 83528C |
Hardness (Shore A) | 65 | 55 | 65 | 55 | 60 | 60 | 65 | 55 | ASTM D2240 |
Tensile Strength (PSI) | 200 | 900 | 180 | 900 | 120 | 600 | 200 | 900 | ASTM D412 |
Elongation (%) | 150 | 300 | 150 | 300 | 120 | 300 | 150 | 300 | ASTM D412 |
Tear Strength (PPI) | 30 | 60 | 30 | 60 | 30 | 60 | 30 | 60 | ASTM D624 |
Operating Temperature (oC) | -55~160 | -55~160 | -55~200 | -55~160 | ASTM D1329 |